Bulkhead-to-Bulkhead
A bulkhead-to-bulkhead inventory is a physical
count of all the material aboard a ship or within a
specific storeroom.
A bulkhead-to-bulkhead
inventory of a specific storeroom is conducted when a
random sampling of that storeroom fails to meet the
inventory accuracy rate of 90 percent.
Specific Commodity Inventory
The specific commodity inventory is a physical
count of all items under the same cognizance symbol or
federal supply class (such as 6515/6505), or that
support the same operational function (e.g., bandages,
IV fluids, needles, etc.).
Special Material Inventory
A special material inventory requires the physical
count of all items that, because of their physical
characteristics, costs, or other reasons, are specifically
designated for separate identification and inventory
control. Special material inventories include but are
not limited to stocked items designated as classified or
hazardous. Physical inventory of such material is
required on a scheduled basis, as prescribed in the
NAVSUP P-485.
Medical supplies are examples of both the specific
commodity and special material inventories.
Spot Inventory
A spot inventory is an unscheduled type of
physical inventory to verify the existence of a specific
item. It is usually conducted when a requisition is
returned showing the item is not in stock but the stock
records indicate the item is on hand. A spot inventory
is also conducted when directed by higher authority or
when a specific item has been found to be defective.
Velocity Inventory
A velocity inventory is based on the premise that
the faster an item moves, the greater the room for error.
This type of inventory is required on items with a
relatively high turnover rate.
Random Sampling Inventory
A random sampling inventory is considered to be
part of the annual scheduled inventory program. It is
done to measure the stock record accuracy for a
segment of material on hand.
INVENTORY PROCEDURES
Proper inventory procedures mandate a complete
and correct item count. You must ensure that the total
quantity of each item is determined as accurately as
possible. Keeping in mind that inventories are
conducted to bring stock and stock records into
agreement, you can see the importance of a complete,
accurate, and legible inventory.
Documents
authorized for conducting inventory counts of stock
material include NAVSUP 1075 (whether or not
maintained as locator records) and machine or
manually prepared listings. Copies of Stock Record
Card, Afloat, NAVSUP 1114, even when maintained in
storerooms, are not to be used as inventory count
documents.
Promptly upon completion of the physical
inventory and before matching inventoried quantities
against stock record balances, review the inventory
documents to ensure that
all items scheduled for inventory have been
counted or verified as nonexistent,
quantities counted are legibly recorded and
compatible with related units of issue,
all locations applicable to the inventory segment
have been checked,
added items are adequately identified and
legibly recorded,
items are documented in National Item
Identification Number sequence, and
documents are dated and initialed.
RECONCILIATION OF COUNT
DOCUMENTS AND STOCK RECORDS
Upon completion of the physical count and review
of the count documents (documents with the actual
numerical count of the items), the next step in the
inventory process is to reconcile count documents with
the stock records. This is done to determine if a
difference exists between the physical count and the
amount recorded on stock records.
When the count documents are correct and
complete, compare them, item by item, with the
applicable stock records to determine whether
differences exist. If no differences exist, post the
matched count cards or items in the inventory listing to
13-16
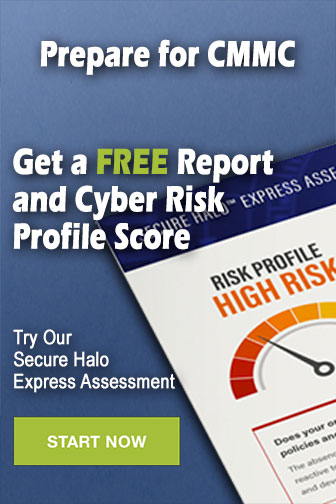